Powering Pharmaceutical Processing
Stainless steel tubing, fittings and fabrications that meet stringent pharmaceutical industry demands to unleash excellence in pharmaceutical manufacturing performance.
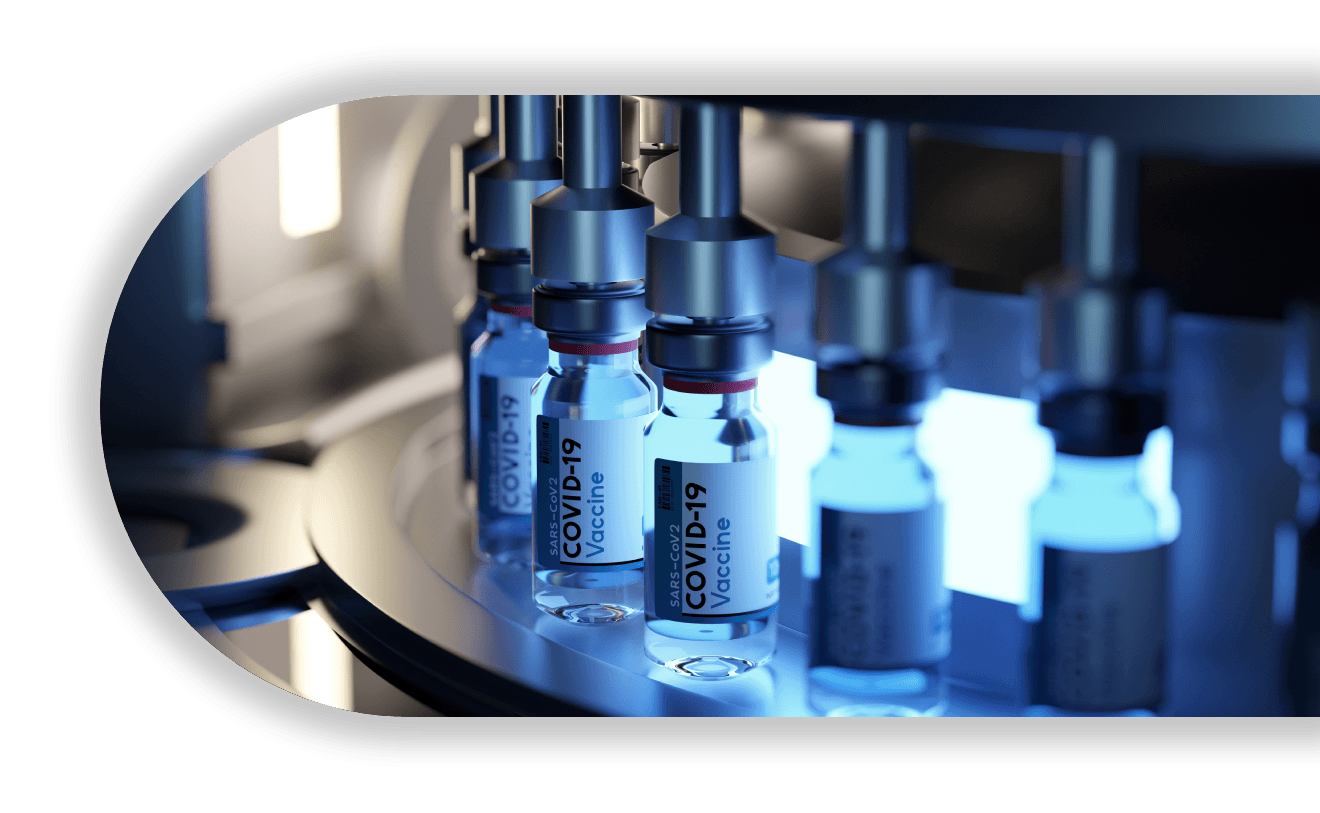
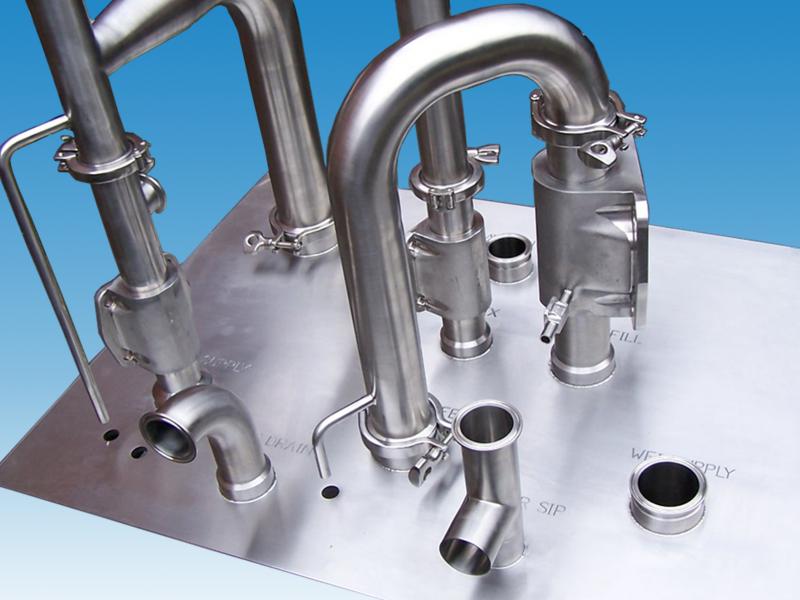
Your Trusted Partner in Stainless Steel Pharmaceutical Fittings
At Stainless Fittings Ltd (SFL), we have been supporting customer initiatives within the pharmaceutical industry for over 75 years through the creation of superior stainless steel tubular products and fabrications. Our unwavering commitment to quality and innovation has earned us a globally recognised position as leaders in meeting the exacting demands of the pharmaceutical sector.
Why Choose SFL for Your Pharmaceutical Needs?
Tailored Excellence for Your Needs
Manufacturing Mastery - 75 Years of Expertise
Industry-Leading Biobore Range
Unwavering Quality Assurance
Tailored Solutions for Your Unique Challenges
We understand the complexities that pharmaceutical professionals face. This deep-seated industry knowledge empowers us to deliver products that are finely tuned to your specific requirements.
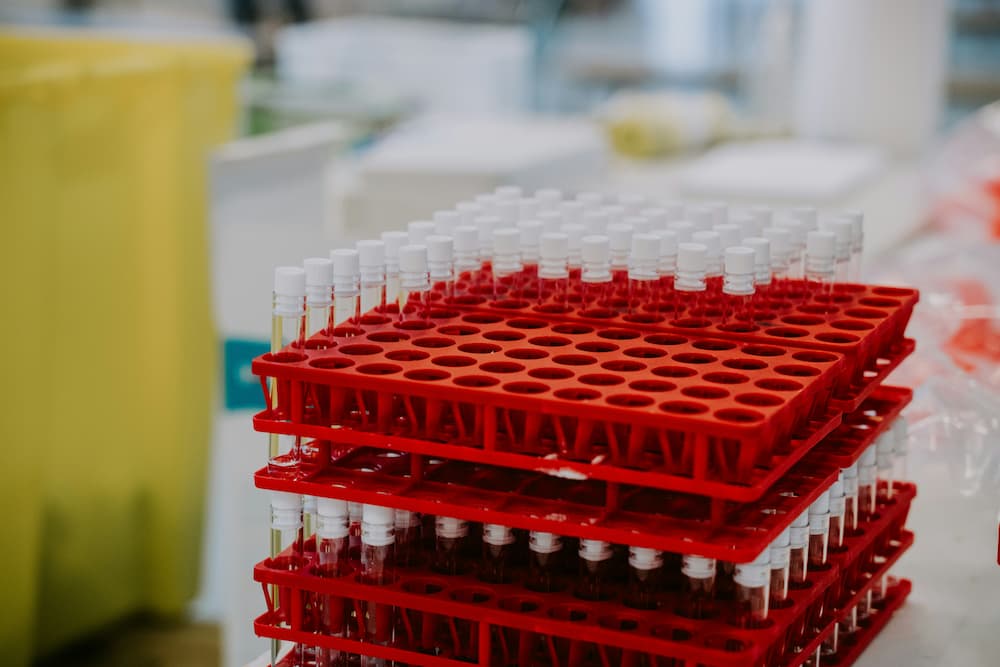
Advanced Manufacturing for Unrivalled Performance
Over the past 75 years, we have continuously evolved our manufacturing capabilities to align with industry advancements. Our dedication ensures that we consistently meet the ever-escalating standards of quality while helping you select the perfect product for your application.
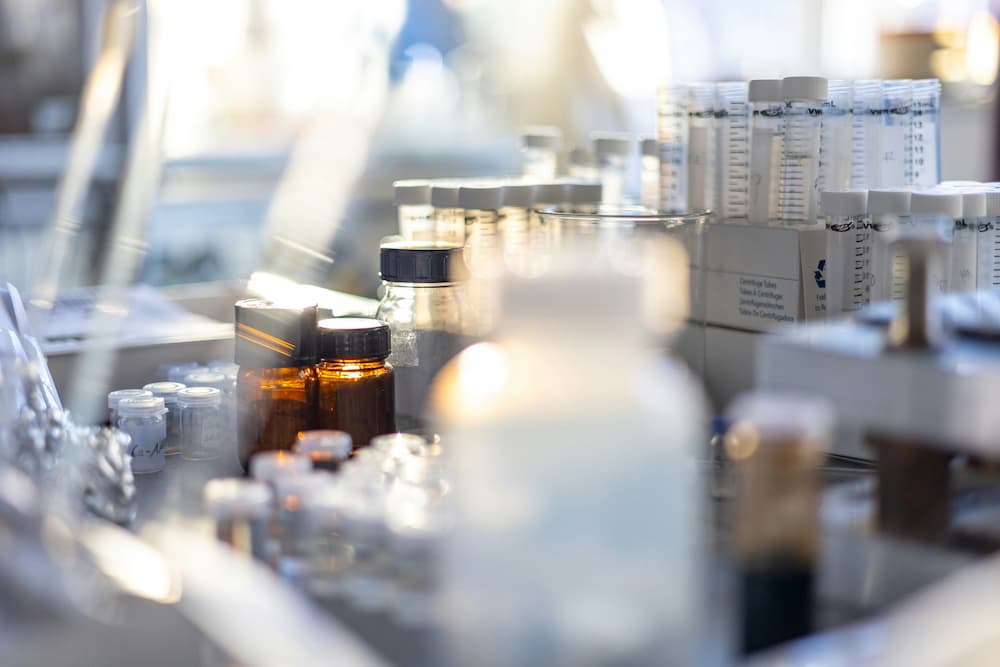
Market-Leading Biobore Range
Your industry benchmark: our renowned Biobore range is meticulously crafted to meet the exacting standards of the pharmaceutical and bio-processing sectors. With unparalleled materials and quality, it stands as the undisputed leader in the market.
Uncompromising Quality Assurance
We adhere to stringent quality control procedures meticulously developed to meet industry standards. This dedication has earned us the trust of blue-chip companies globally, who rest assured knowing that our Biobore tubes and fittings comply impeccably with FDA requirements.
Our Commitment to Excellence
Our rigorous quality control process encompasses comprehensive recording of each component’s chemical and mechanical analysis, ensuring adherence to industry specifications (ASME BPE). Employing the closed head orbital weld method, we generate weld samples that prevent installation challenges, guaranteeing a seamless process on-site. Every SFL product is marked with a heat number, and our fully traceable material certificates provide you with absolute assurance.
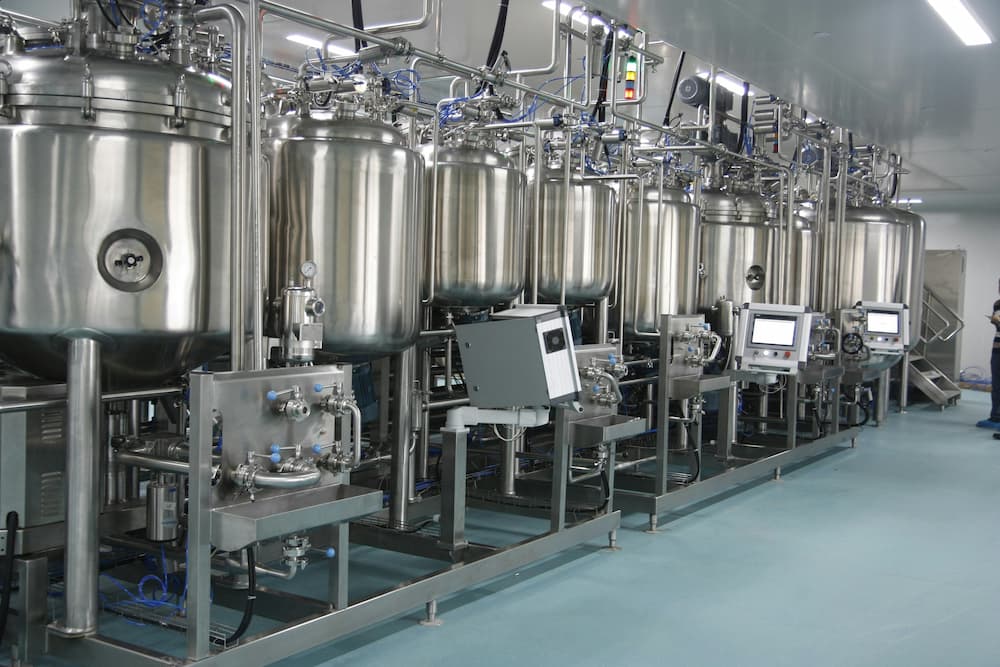
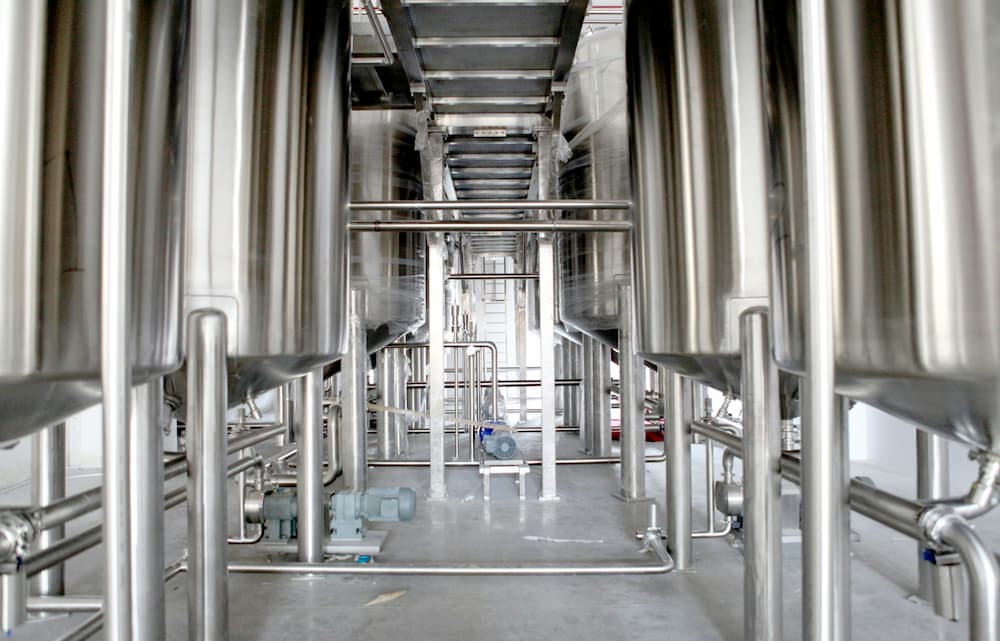
Our Industry Alignment
Our tubing adheres to the stringent standards of ASTM A269 and ASTM A270, boasting controlled sulphur levels and tolerances prescribed by ASTM A270-S2 supplementary requirements. All our materials are meticulously crafted from T316L stainless steel. Biobore fittings are intricately manufactured to ASME BPE specification dimensions and corresponding tolerances.
HOW IT WORKS
SFL is dedicated to solving your pharmaceutical manufacturing challenges. Discover 3 steps to pharmaceutical processing success.
- 1. Get in touch and tell us your pharmaceutical manufacturing requirements.
- 2. We’ll find the perfect tubing, fittings and fabrications solution for your needs.
- 3. Enjoy enhanced pharmaceutical processing performance.
Crafting Excellence Through Innovation
We recognise the significance of special finishes in high-purity and WFI (water for injections) applications. To address this, SFL offers a range of finishes meticulously tailored to meet the diverse requirements of most applications.
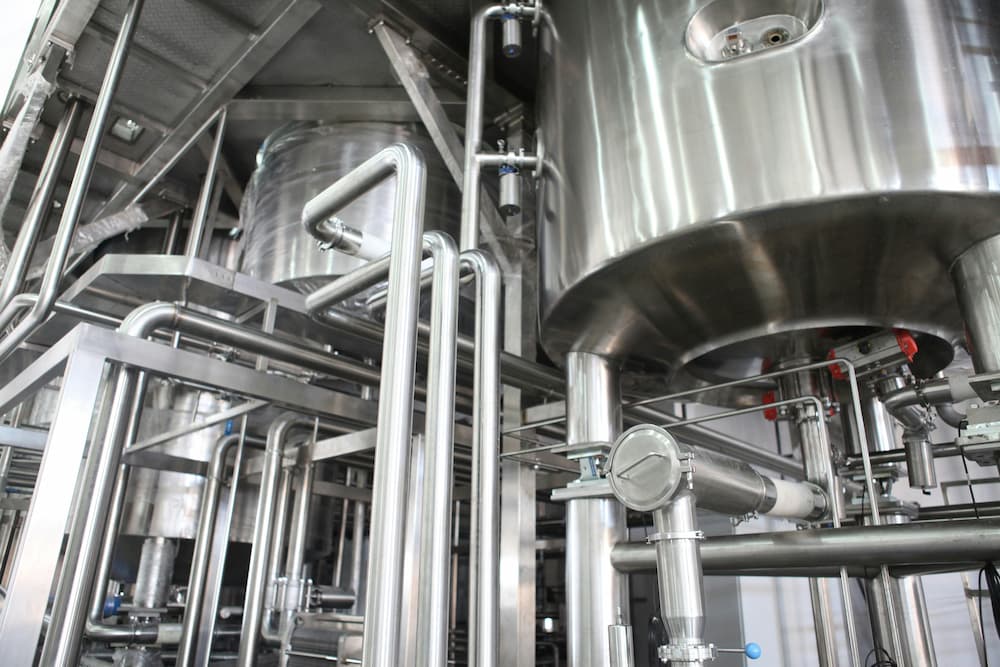
Elevating Your Projects Beyond Expectations
Benefit from our pharmaceutical industry expertise by accessing pre-fabricated spools designed to your specifications. Count on us to offer insightful advice on your designs and to expertly craft high-quality skid units and flow plates. Our team of qualified welders adheres ASME IX, Manual BS EN ISO 9606-1 and Orbital BS EN ISO 14732 standards, ensuring unparalleled quality in every aspect of your project.
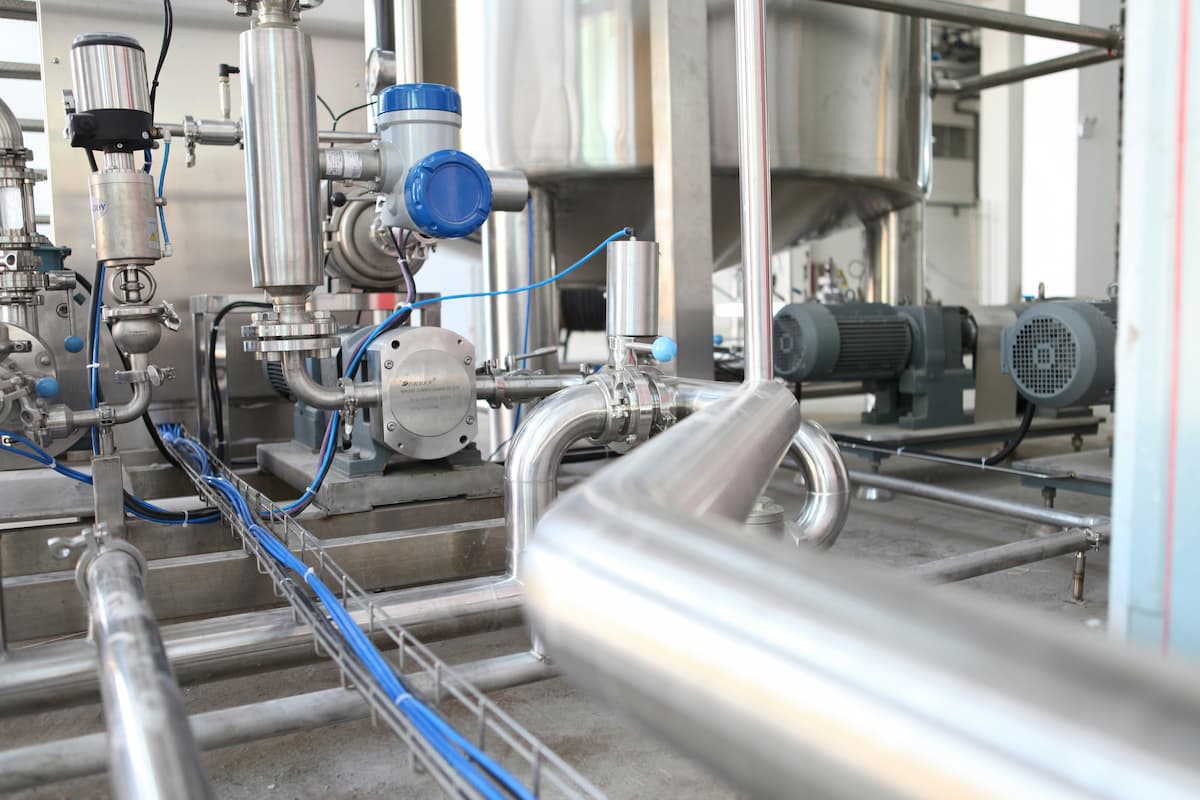
SFL can offer a wide range of services for your products including:
- Annealing
- Electropolishing
- Passivation
- Pickling
- Honing
- Borescope videoing
- Surface finish certificates
- 3.1 material certification
- Dye penetrant testing
- Hydrostatic testing
- X-ray testing
- Weld logs, maps, and qualifications
- Welding Gas bottle and batch certification
- Dye penetrant testing
- PMI testing
Our SFL Biobore Range
Enhance hygiene, improve efficiency and maximise performance in your pharmaceutical manufacturing process.
Ready to Unleash Pharmaceutical Excellence?
Contact us at 0121 387 3229 to explore the transformative possibilities that SFL brings to your pharmaceutical endeavours. Step into a realm where precision meets perfection, and where your aspirations become our mission.